There are many factors that impact the economic competitiveness of a new pharmaceutical company. However, together they amount to minimising both time-to-market and costs while remaining compliant with all regulatory standards and requirements. A key component of this is ensuring a reliable, compliant supply of the API. How can an experienced CDMO like Dapin assist?
Perhaps the most obvious factor is to keep input costs down. Yes, part of this involves sourcing cost-competitive raw materials and reagents, but that’s only part of the story. Using more efficient processes can also save significant money. Here at Dapin, we always look closely at all processes as they enter the plant, and try to minimise waste and optimise our resource utilisation. Cutting energy consumption can also have an impact – if a reaction can be run efficiently at a lower temperature, for example, or for a shorter time, less energy will be needed, further reducing costs.
But economic efficiency is not solely about minimising costs. The faster a new drug can reach the market, the sooner it will start to repay the investment the company has made in it. The more quickly a viable process can be identified and optimised, the sooner a molecule can enter clinical development.
Any savings must be achieved while also meeting all regulatory requirements for quality and compliance. It’s something that our team here at Dapin is extremely well versed in, thanks to our long-standing expertise and experience. As well as having a solid grounding in GMP and other regulatory requirements, our experts know how to spot and remediate any issues that might occur. Their insight gained from earlier projects and campaigns is invaluable.
A high level of process optimisation is another way to help maintain cost control. In some functions, such as quality control, there is the potential for a high degree of automation of processes. Other areas may require more creative thinking if lean manufacturing is to be achieved.
We should continually be thinking about how we might do better. How might a process be made more reliable, more efficient, more streamlined? And, of course, savings in one area may well lead to knock-on savings in others. A more intensive process that uses less solvent, for example, will not only cut solvent costs, but it will also generate less waste, and make the whole process more sustainable. Even good relationships with suppliers can make a difference.
In fact, relationships across the board are important. In my experience, a close collaboration between our team and the client’s team will always make the entire development process for an API run more smoothly. There will always be hitches and challenges in any development process, and if everyone is working closely together, it will usually be possible to sort them out at a very early stage, and less time would be lost than if the two teams were operating in individual silos.
The amount of process development work requires will, obviously, depend on the phase the project is in. If it has just been passed on from the medicinal chemistry team, the synthetic route is unlikely to be feasible on a commercial stage, and even if scale-up work has begun, the process will rarely be as robust as one that is ready for Phase 3 trials.
We are able to support our clients in every phase of development, including both process development and the analytical methods that will be required to prove the API’s quality. And, of course, the validation of the process and methods that will be required in the late stages. Any process that is developed to manufacture APIs or late-stage intermediates will require careful validation, with the documentation a part of the dossier submitted to the authorities for approval. This will ensure the process makes the product in the required quality every time.
We will ask our clients what level of support they will require, and will have regular meetings with them to ensure everything stays on track. The support and input a small biotech company’s team requires will be different from the amount needed by a big pharma company, but equally, the learning will go in both directions there as their team will also have a lot of relevant knowledge about the molecule .
A face-to-face on site meeting early on is really important for fostering that close relationship, which is now becoming routine again after the restrictions imposed by Covid. We can really see the difference it makes, and the better lines of communication it creates that enable us to make products more quickly and cost effectively, while meeting all quality demands.
Author
DR. STEPHAN SECK
Managing Director
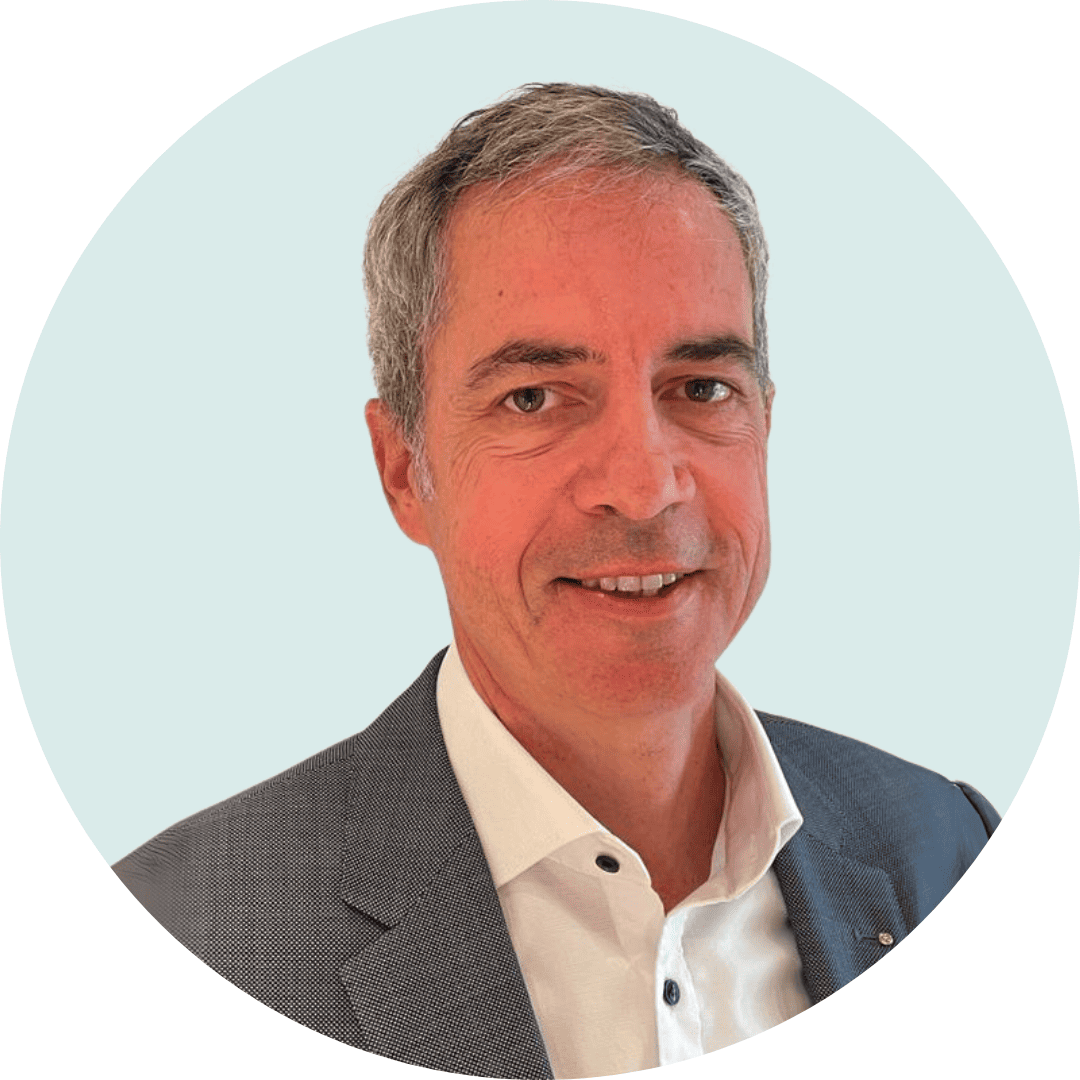
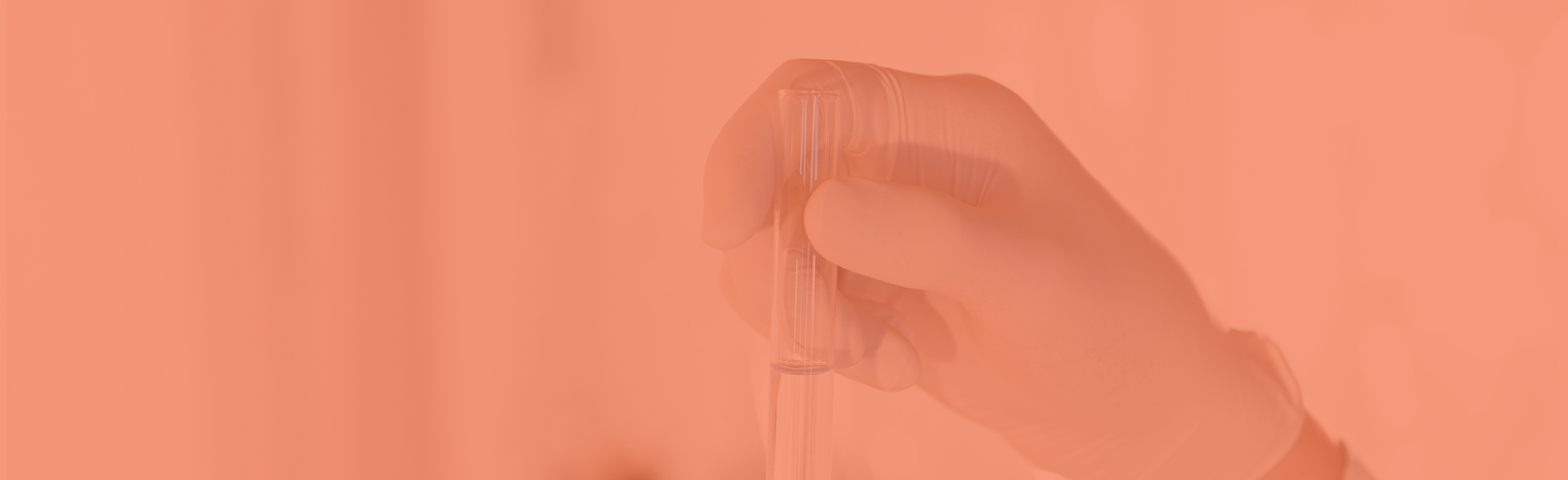
Contact Us
Contact us today to explore reliable, end-to-end API and
Intermediates solutions tailored to your needs.