By Yvonne Hellwig
A robust quality system is essential for any company that manufactures pharmaceutical products. This quality system will ensure that all of the components in a medicine, including the active pharmaceutical ingredients (APIs) we make here at Dapin, are safe. It means the APIs we produce will have the quality that our customers expect, and that the Good Manufacturing Practice (GMP) guidelines have been strictly followed.
First, all raw materials used to manufacture APIs are purchased from qualified suppliers. Our quality control department will carefully analyse these raw materials to ensure they are indeed of the required quality, and no contaminants are present that might cause problems later on.
Vendor qualification
We will qualify all our vendors before ordering the raw materials used for API production. If the material is classified as a critical raw material that has a significant impact on API quality, supplier audits are also required. While the GMP requirements are less strict in the earlier stages of an API’s, everything used in the process will still need to comply with our quality system.
Only after this qualification process has been completed successfully will we know that the vendor is reliable. We need to be sure that the supplier’s own quality system matches up to what we require, and that they will provide us with all the documentation we will need to back up our own records, such route of synthesis or BSE/TSE certificates, and also nitrosamine statements.
This is not a one-off task for each vendor – it is an ongoing process. We will still check every delivery from that vendor to verify that it still meets the required standards. Is the packaging clean? Is the labelling correct? And does the batch number tally with the one on the paperwork? We requalify our vendors every year, and as part of that process we keep track of how successful each delivery they sent us was, including compliance with deadlines and accurate quantities, as well as that all-important quality.
GMP compliance
The second important factor in a quality system is to ensure we follow all GMP rules to the letter, and that we are working to the most recent versions of the guidelines. These guidelines are not static, and the quality assurance team will ensure any changes made by bodies such as FDA, EMA or ICH are implemented here.
All our processes must meet these requirements. We must ensure the materials delivered to our customers are in full compliance, and that there is batch-to-batch consistency. Equipment must be well designed and properly maintained. Where cleanrooms are required, these need to be carefully controlled, with real-time monitoring of all critical parameters to prove they remain within the specified ranges. And all staff must be properly trained and qualified.
Analytical testing is an important part of the quality system. Testing is performed by the quality control department. For products in Phase 3 clinical trials and for commercial supply, the analytical methods must be fully validated according to ICH standards. This validation makes sure the methods are specific, accurate, precise, linear, robust, and that they can detect even small amounts of any impurities.
The stability of the solutions used in the method will need to be studied, too. How long can they be used before they degrade? If a solution has degraded after, say, two hours, the method is unlikely to be sufficiently robust as most analyses take longer than this. But if it is stable for a couple of days, that will be fine.
New method development is perhaps the most interesting aspect of quality control. It can resemble detective work, looking for and identifying any impurities, and then finding an appropriate method to detect all of them.
For some APIs, microbiological and endotoxin testing will be required, too. Stability tests are also essential, as these will help determine the drug product’s shelf-life. We also need to validate all cleaning procedures, particularly when equipment is used for multiple different products. Any carry-over of material from one product to the next would cause a significant contamination problem.
Accurate record-keeping
And, of course, we have to carefully document everything we do, noting any changes that are made to a process and ensuring these changes are approved. It’s vital that we spot any deviations early so we can intervene immediately.
We check batch records and analytical test records to make sure everything has been carried out correctly. Audit trails from every computerized system will show what was done by whom, when, and why. This will help us track any divergences. Any deviation must be noted and shown to have no impact on product quality. For the continuous improvement of processes, the root causes for any deviation must be found and resolved.
These are just a few of the factors that are important when developing a robust quality system. Ultimately, the system is designed to ensure that the API is the same every time, meets all required regulatory standards, and will be safe to be taken by patients.
Author
Yvonne Hellwig
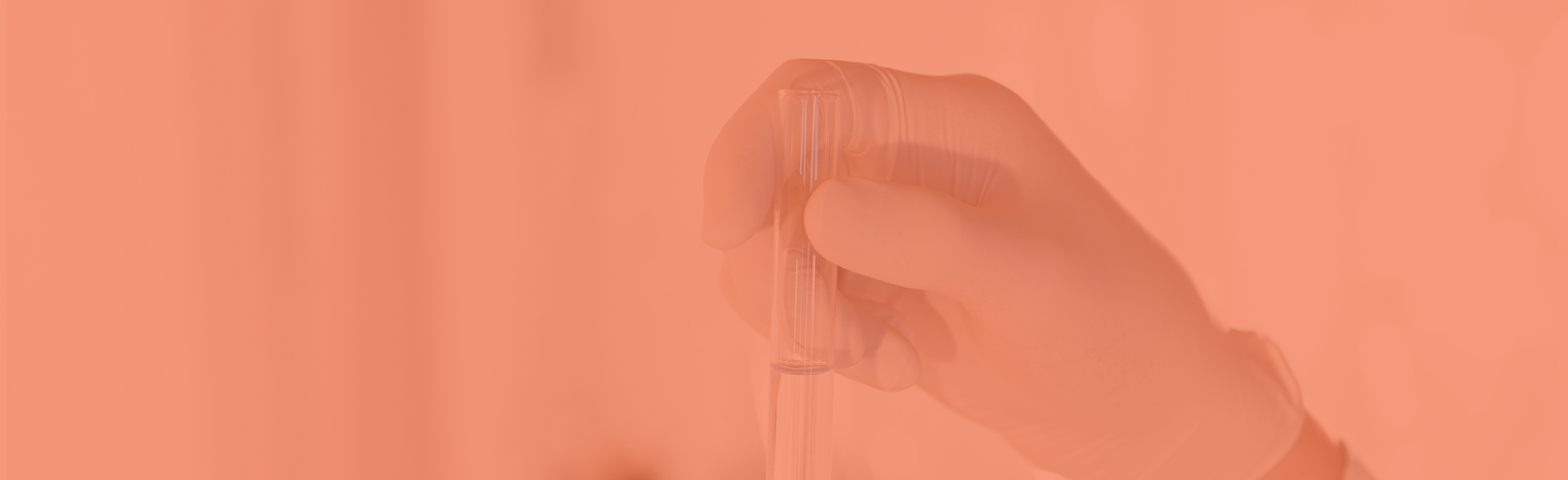
Contact Us
Contact us today to explore reliable, end-to-end API and
Intermediates solutions tailored to your needs.